Been busy working on a few aspects of SS Chai. For one thing, with TLAAG as design partners, we have a design proposal. If anyone is interested in reading… we’ve created a long proposal as well as an “executive summary.”
Here’s a really topical overview:
Sampan Super Chai is a prototype for a floating art/science platform that addresses both local and global concerns of climate, citizenship, and the ecosystem. It drifts from downtown Portland to the Columbia as a tethered cluster of floating modules. Participants investigate the rivers’ tangled relations, becoming familiar with the comprehensive, “dark ecology” of the present.
Sampan Super Chai provides hands on encounters with the river in three structured ways:
Process: Using the river to produce and drink tea together, as a hands-on encounter and convivial activity
Observe: Empirical citizen science, in both short and medium length encounters
Imagine: Placing the present within the larger ecosystem context, and a span of Deep Time
TEA: Central to the public-facing aspect of Sampan Super Chai is the process of making and drinking chai: cleaning water from the river, making clay cups from its banks, and infusing herbs from the shoreline, while using black tea transported from across the Pacific.
MATERIALS: Modular structures incorporate plastic flotsam from the Pacific. As counterpoint, the floating rafts and buoys are made from mushroom mycelium (fungal threads). Mycelium material is molded to replace Styrofoam in building and packaging materials.
Here are a couple of facets of the project:
BUOYS.
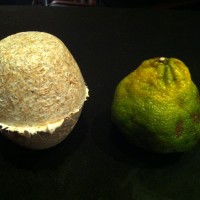
Buoy grown from Ecovative’s GIY pre-inoculated mycelium + substrate mix
I’ve started a work group with my ITP colleague Eric Rosenthal and 4 students – Erika Miller, Ken Amarit, Kina Smith and Laura Juo-Hsin Chen – on a prototype of the “data buoys.” These will light up the project at night, in a magic act of dematerialization:)
We’ve taken apart garden lights and are using a combination of solar cell, battery, and bright LED light. I am currently prototyping a buoy made of mycelium, which would grow around a plastic water bottle, which would be weighted at the bottom, and contain all the electrical components at the top. This way the buoy contains all the elements we’re talking about – plastic waste, petroleum, renewable energy, and mycelium / ag waste material. I think we can make the buoys out of a sawdust-eating mushroom, if we want to get Northwest with the project. Or Willamette Valley ag waste would be great too.
CLAY.
Masters candidate Talya Stein has been working with the clay I brought back, at NYU Steinhardt’s Ceramics Dept. under the tutelage of the Chair, Judy Schwartz and the Kiln Master, Shida Kuo,
These slabs each represent a mix of the hand-dug Willamette R clay amended with mined ball clay, from 10% – 50% amendment.
Here is the break down from Talya:
1. Dry the clay and break it up to little pieces.
2. Make powder out of the clay.
3.Add water gradually and mix.
4. Let the clay dry a little.
5. Make a lump out of the clay
6. Measure precise amount of the clay and the Ball clay.
10% increments. (10% = 5g)
7. Make sure not to mix anything up! 10% Ball clay, 90% Mud = 5g Ball clay, 45g Mud…
8. Wedge balls together.
9. Make Tile tests (Making them look like little tomb stones is optional).
These were bisque fired at Cone 6.
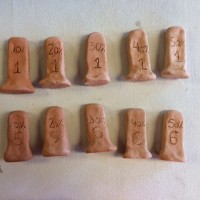
The 9:1 ratio held up as a slab, so we thought we could try 100% river clay, now that we understood how to process the clay correctly (completely dry and pulverize, weigh, add water slowly, wedge long and well).This had similar issues to my tests in Portland- cracking, falling apart, not enough elasticity.
Next step was trying the 9:1 river/ball clay mix as cups:
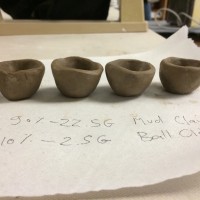
These are getting fired on Friday.
Next steps get a little confusing to me.
Judy Schwartz, Chair of Ceramics at Steinhardt, had this exchange with Talya:
Future steps:
1. Test the water absorbent of the clay
If the clay is fired to a higher temperature, the clay can become vitrified..meaning the clay becomes almost like a glaze and is not absorbent of moisture. The lower the fire or heat, the more porous the clay. That is why flowerpots are such good vessels for plants because water evaporates easily through the pores of the clay. We can run a sample of the 100% mud clay as you call it, in the high fire kiln and see if it melts….when it gets this hot….2300 F… this clay would probably melt and be totally non porous. The next high fire will be next week or email Shida and he will put the sample in the kiln to see if it melts or if not you will see how there is no porosity. Make a sample at home and bring it in to put into that kiln but put it inside a high fire clay bowl in case it melts out flat.
2. Glaze–
for low fire ..yes, that is fine.
3. Test if the water gets toxic
I guess you mean from a glazed sample cup?
If you want to test toxicity of the clay I guess you would take it to a lab before and after firing.
4. Test the breakabilaty of the mugs
I do not know a test for this….
but what do you want to accomplish knowing how much pressure it takes?
Does this make sense? Do u think we should be doing anything else?
5. I tried to explain to Marina what you told me about taking out the iron from the clay.
Your mud clay looks like a standard clay found around river beds…containing a fair amount of iron oxide making the clay fire red… it is called an earthenware clay.
We use earthenware in the studio too, but I use a refined earthenware paying extra to have the iron oxide removed so that the students have a cleaner body to glaze on. When you mixed yours with mine, you can see how the clay got lighter and lighter because there was less a percentage of Iron Oxide in the clay body.